OEM Custom Rotomolding Bluetooth Plastic Speaker Enclosures
Bluetooth speakers are gaining popularity thanks to their stylish shapes and visual appeal colors. Rotmomolding is an ideal plastic manufacturing process that produces a hollow product of all shapes and sizes. This extremely versatile is a great fit for bluetooth speaker enclosures.
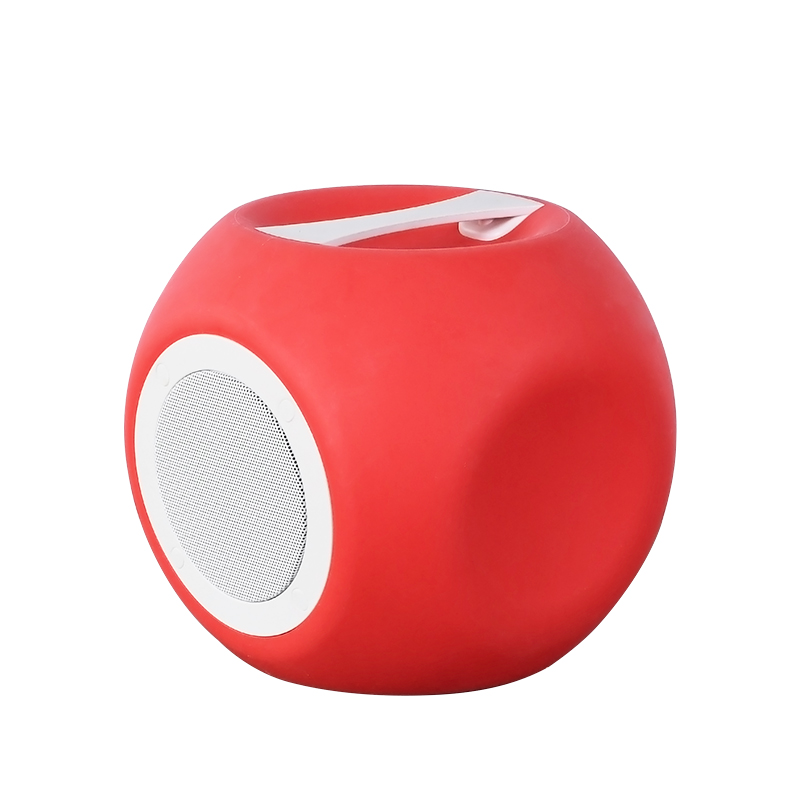
How does rotomolding work
A measured amount of plastic resin power is loaded into the mould, and then moved into an oven where a microprocessor controls the temperature, blower velocity, bi-axial rotation and molding cycle. As heat penetrates the mold, the resin melts and adheres to the mold's inner surface until it is completely fused – no pressure is involved. The simultaneous heating and rotation evenly distributes the resin to the inner surface of the mold, maintaining a uniform wall thickness. The mold is then transferred to the cooling chamber for curing. The cooling cycle is controlled to optimize the final product’s impact strength and performance. After the molds have been slowly cooled with air and water and the part has cured to achieve its maximum impact strength and physical properties, the part is then removed from the mold to be trimmed, imprinted and assembled.
Benefits and advantages
- 100% lightweight, recyclable polyethylene, variety of colors and options
- Low mould costs, roto mould is about 1/3 to 1/4 of the cost of blow moulding and injection mould for the same product,
- Unique design and structural capabilities for simple or complex shape
- Single-piece product design - seamless, free of joint, consistent wall thickness
- Protected against dust, UV, temperature, water, corrosion & vibration
- Molded in hardware inserts, branding logo
Light Venus has been dedicated to helping customers design, develop, and produce an array of custom roto molded products since establishment. We have all the expertise and experience necessary to make your project a success. With over 15,000 square meter of manufacturing space, more than 500 motivated people, we can ensure that you will receive top quality products in a very timely manner.
For more information on how we can fulfill your custom bluetooth speaker enclosures needs, please call us, use the online form to leave us message, or email us to roto@lightvenus.com, we will get in touch with you promptly!