OEM Custom Rotomolding Service Of Plastic Speaker Enclosures
Plastic speaker enclosures are now very prevailing and dominate the commercial and consumer market. Plastic is light weight, durable and offers the speaker designers more flexibility to produce aesthetic shapes and stylish colors. The choice of thermoplastic is polyethylene thanks to its its excellent impact and chemical resistant properties. The manufacturing option is highly versatile and cost effective rotomolding process.
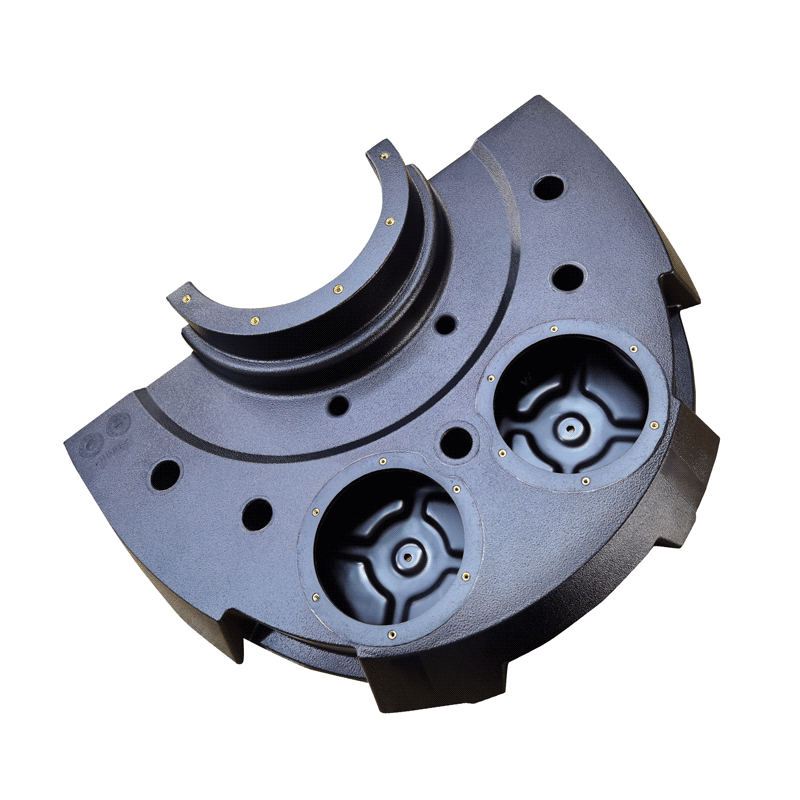
Explanation of Rotomolding
Rotomolding, rotational molding, or rotocasting is commonly known as an ideal process to produce hollows products. Unlike other plastics molding processes such as injection molding, thermoforming or even blow-molding, the manufacturing process does not induce any pressure. Because of the lack of pressure in the process, roto-molded poducts are far more durable than products crafted from the other molding processes, namely injection molding, compression molding, blow molding or vacuum forming.
Rotmolding process details
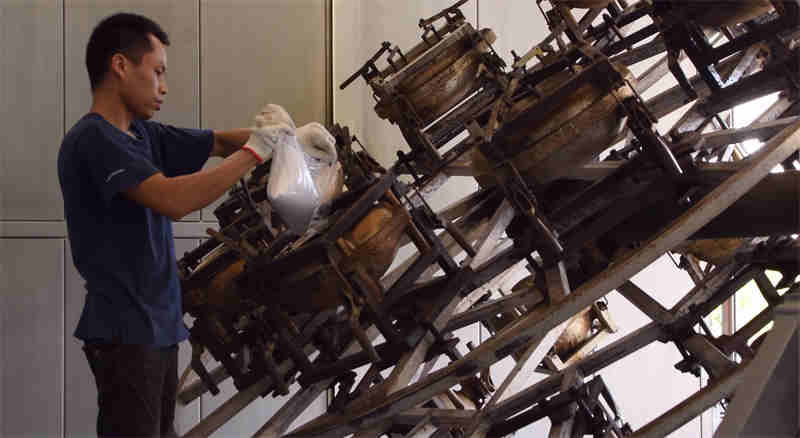
1.Mold loading
Rotomolding starts with a quality metal mold that is placed on an arm of a rotating molding machine that has a loading and unloading area, a heating oven and a cooling station. Several molds may be placed on the machine at the same time.
2.Material Feeding
The exact type and amount of resin are dictated and measured by the products predetermined formula based on the desired wall thickness and other characteristics. The plastic powder resin is loaded into each mold. The mold is then clamped shut. This is also called the charging phase.
3.Melting
The molds move into the oven where they are slowly rotated on both the vertical and horizontal axis. As heat penetrates the mold, the resin melts and adheres to the mold's inner surface until it is completely fused – hardly pressure is involved. This low-pressure method allows the molten plastic, which may be enhanced with corrosion and static resistant additives, to coat the interior walls of the mold cavity evenly. The simultaneous heating and rotation evenly distributes the material on the inner surface of the mold, maintaining a consistent wall thickness.
4.Demoulding
The last step is to reopening the fully dried mold and manually removing the new plastic part, and the mold is ready for the next cycle.
5. Trimming
Some products require technical trim jigs for the secondary finishing operations of assembly, such as routing, riveting of hardware, and then the products are completed.
Main features of roto-molded plastic speaker enclosures
- The mold cost is low. Fo the product of the same specification and size, the cost of roto mould is about 1/10 to 1/3 of the cost of blow molding and injection mold.
- One-piece construction, no weld, joint free, uniform wall thickness, fine surface detail.
- Design flexibility allows for any intricate curve and contour.
- Excellent airtight and watertight properties to protect circuit against the effects of moisture, corrosion and oxidation.
- Moled in threaded insert standoffs to the interior of the plastic enclosures for the mounting of electrical components and PCBs, which saves the cost of secondary operation.
- Molded-in color scratch-proof graphics for branding recognition.
- Polyethylene is resistant to most chemicals and solvents, fully UV protected for outdoor use. can be tailored with flame retardants.
The advantage to works with Light Venus
Light Venus full services for our OEM customers in their kinds of projects, from products design and production.
- Stable production capacity based on the site of 15000㎡ manufacturing space
- More than 500 motivated and highly trained employees
- Technical support from Roto Molding Association
- International quality management ISO 9001 certification
- Highly specialized engineering team with rich knowledge and experiences
- Efficient development, exquisite appearance, precise size control
- 99.9% customer satisfaction
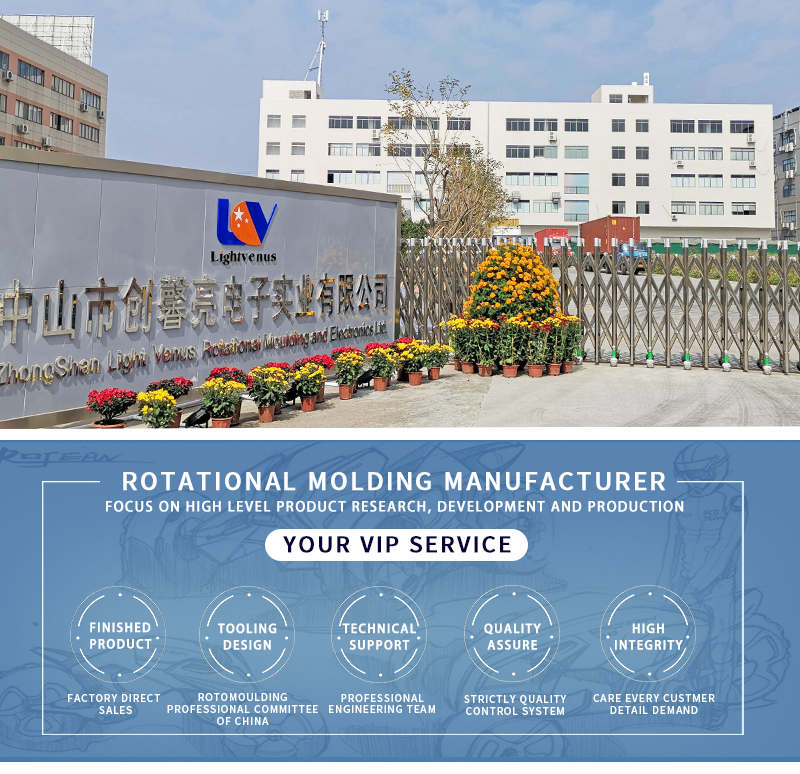
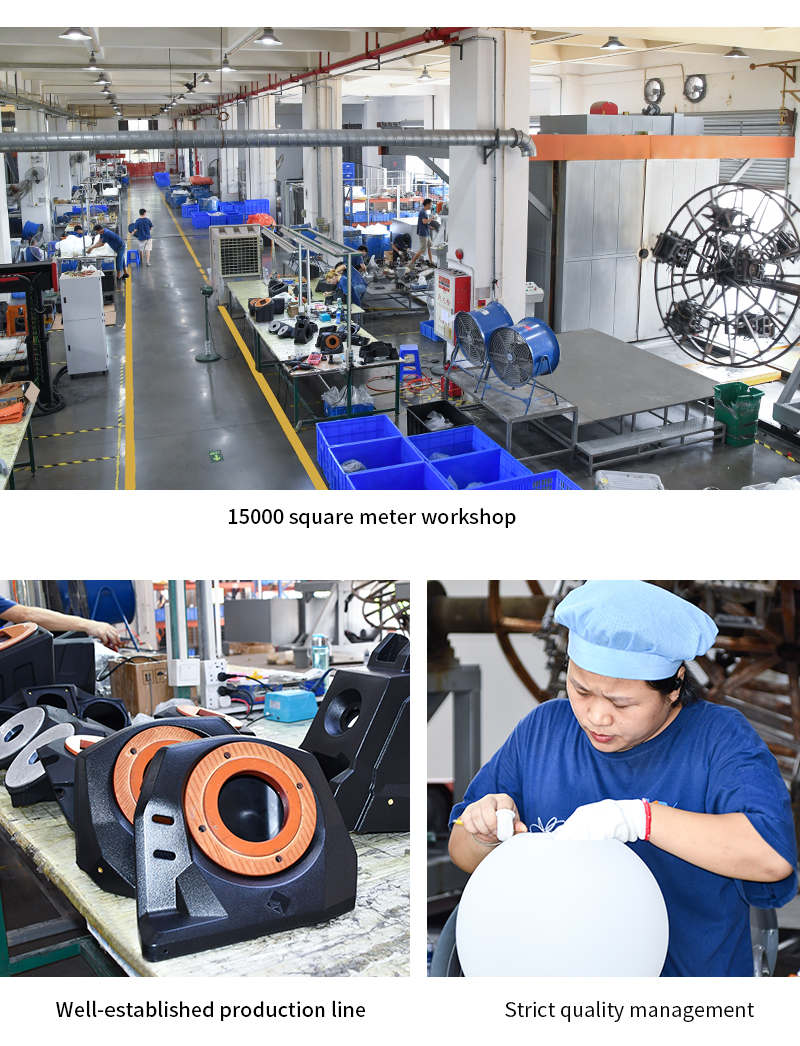
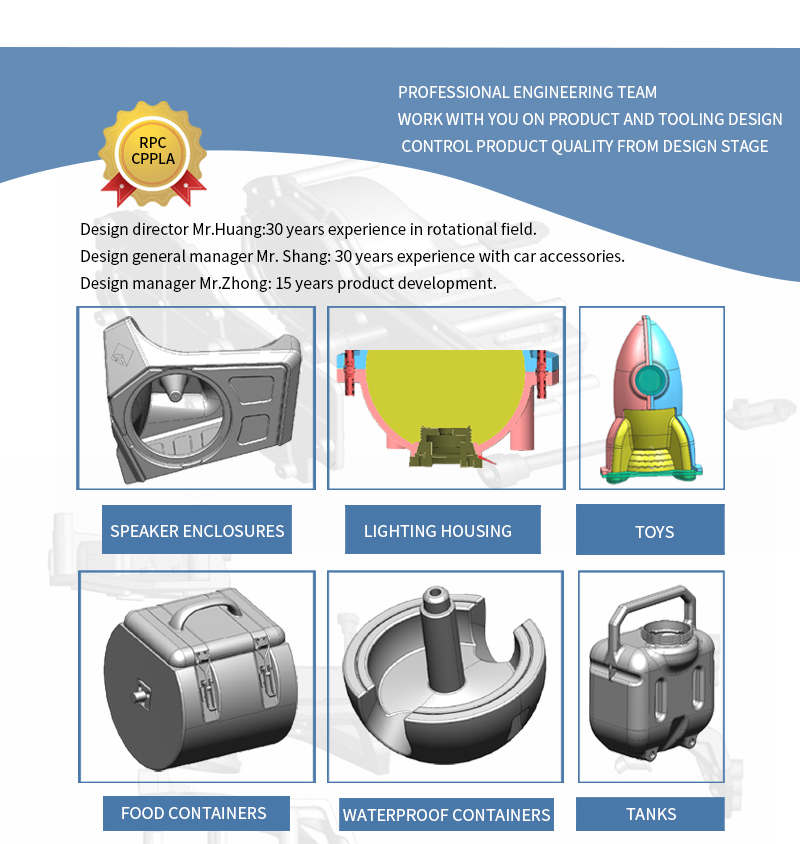
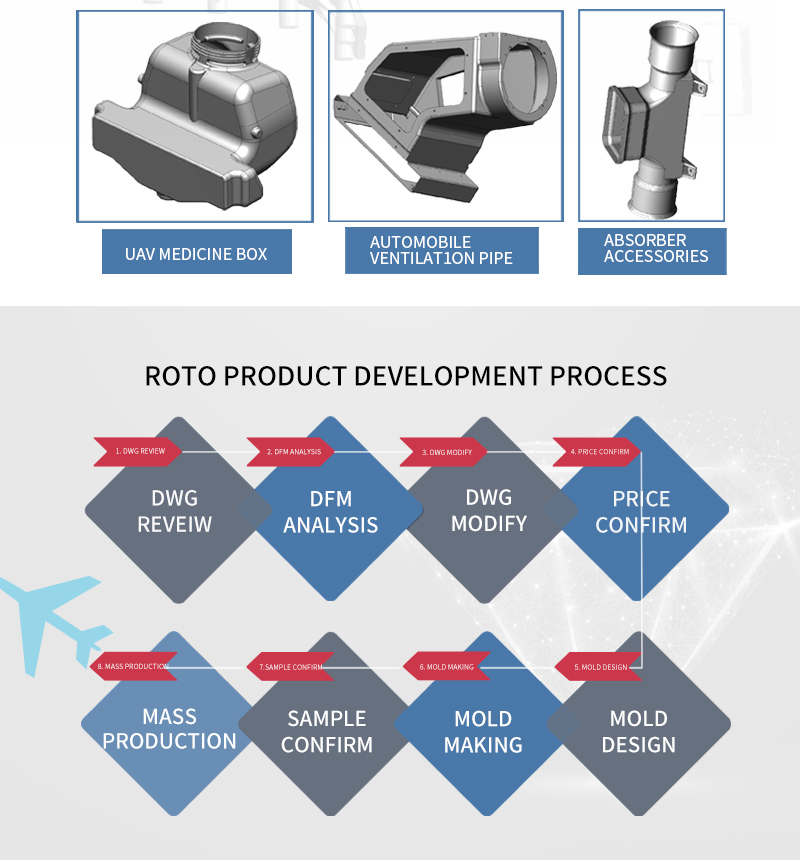
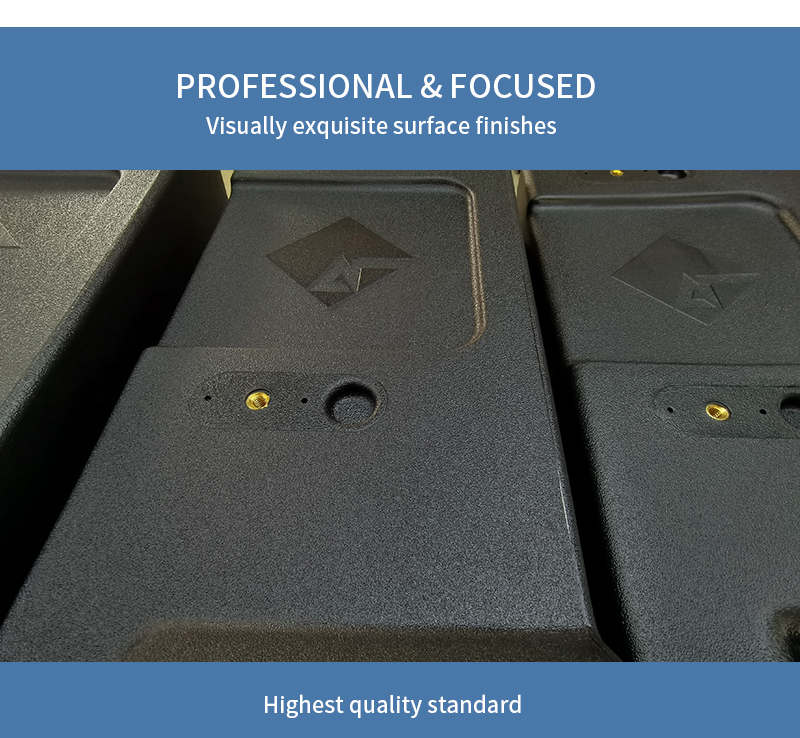
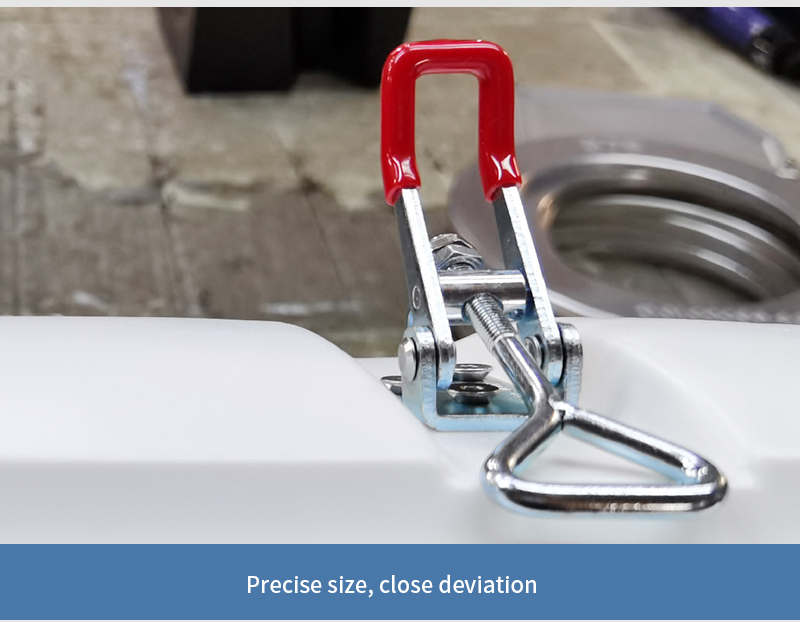
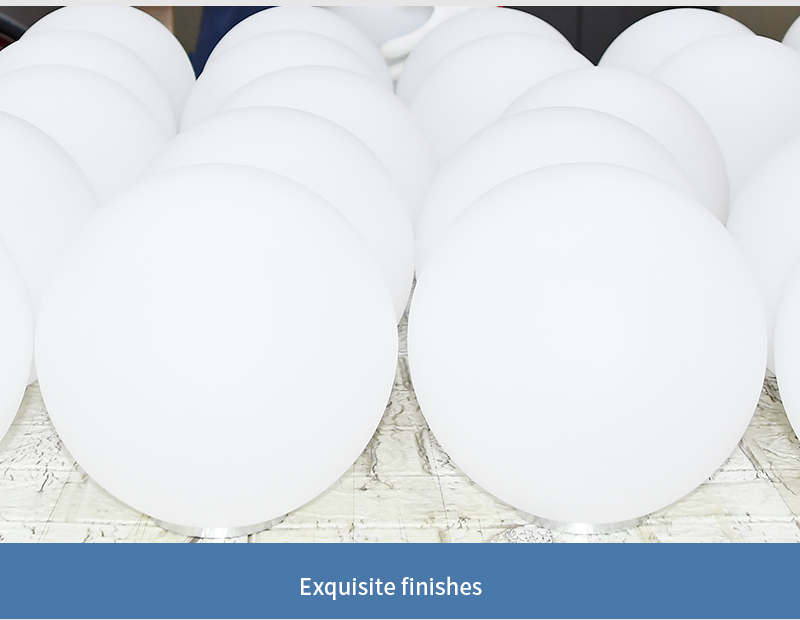
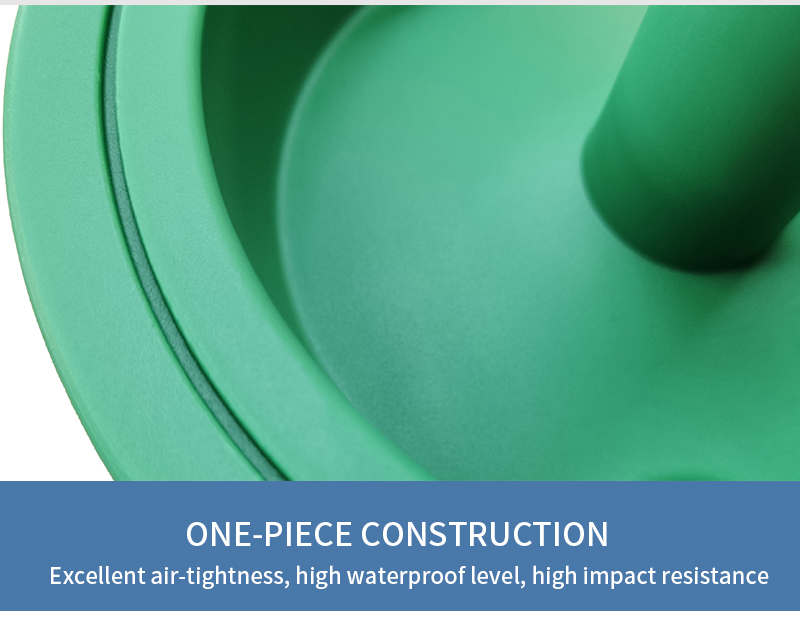
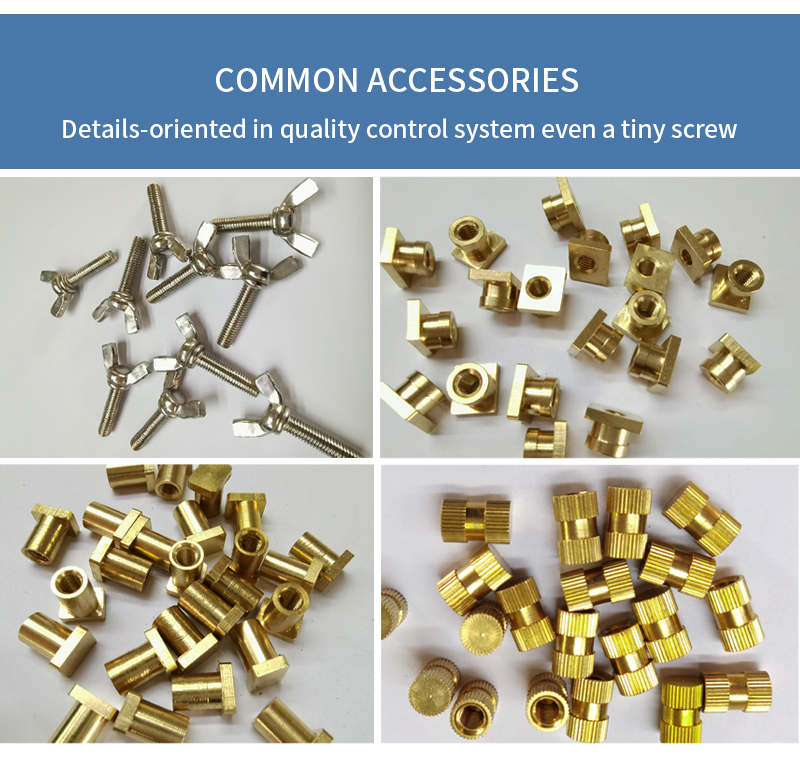